Case History Groppalli srl
SOLUTION: ENERGY MONITORING OF FACILITIES
SECTOR: ENERGY MANAGEMENT
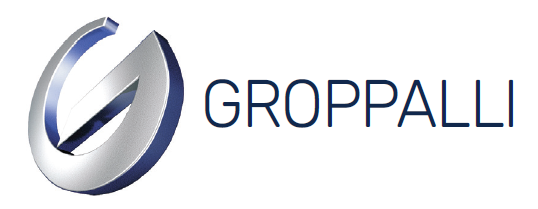
SOLUTION: ENERGY MONITORING OF FACILITIES
SECTOR: ENERGY MANAGEMENT
Groppalli Srl was founded in the 1970s as a small mold manufacturing company, gradually developing the technical expertise to become a leading company in the boiler accessories sector. In 2010, G.ALL was established to supply the group and the internal market with ALUMINUM PROFILES.
In 2016, the Groppalli ALUMINUM SHUTTERS PROJECT was launched, a brand symbolizing quality, professionalism, and innovation, and the company expanded its largely automated production to the shutter market. In 2022, Groppalli opened the new D.E.A. plant (Aluminum Extrusion Division), positioning itself as one of the main European players in the production of extruded profiles in various alloys for all aluminum application sectors.
Groppalli Srl needed to keep energy consumption under control to ensure operational efficiency and automate alarm management in case of malfunctions and anomalies, minimizing downtime. The main challenge was to have a reliable and continuous system for energy monitoring, enabling informed and timely decisions.
This solution has already been successfully used by the Research and Development team for monitoring prototype energy storage technologies. With the acquisition of the new plant in Borgonovo (PC), dedicated to the production of aluminum profiles using an innovative extrusion plant, the need for precise energy consumption control became even more crucial.
Rilheva IIoT platform allows continuous monitoring of energy consumption, offering detailed analysis and KPIs, such as statistics, averages, and energy consumption analysis. These data are broken down by various departments, providing a clear and accurate view of the company’s energy efficiency. Moreover, Rilheva facilitates the automated management of alarms in case of malfunctions or anomalies, improving responsiveness and preventive maintenance.
Subsequently, information related to the photovoltaic system was also integrated, allowing for monitoring of energy savings and detecting any issues or efficiency losses.
The Ewon Flexy 205 gateway collects both energy data via the Modbus protocol from ABB devices in the electrical panel, and production data provided by the Cometal extruder.
Adopting the Rilheva platform offers numerous advantages for Groppalli Srl, making data management and monitoring more efficient and centralized:
• A single system for data management
• Integrated Dashboard with detailed widgets and charts
• Real-time management of historical data
• Comparison of recorded consumption with billed consumption
• Energy consumption analysis to identify unwanted latent consumption
• Cos-phi analysis for continuous monitoring of electrical performance
• Scalable and flexible, ready to connect with future expansions of the production plant and for monitoring other utilities such as gas, water, and hydrogen.
• Enabling technology for the Industry 5.0